Coding regulations for medical devices
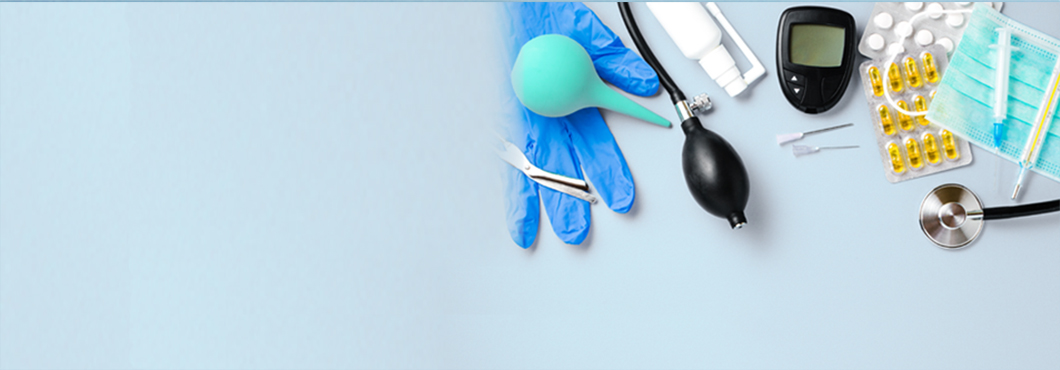
Coding regulations
The Unique Device Identification (UDI) system is intended to facilitate the traceability of medical devices, significantly increase the effectiveness of post-market safety-related activities and enable better surveillance by authorities, by allowing the unambiguous identification of a specific medical device on the market.
To this purpose, the UDI regulation requires that the medical device itself (for reusable products) and all higher levels of packaging must be marked with a unique UDI code in machine-readable (bar code) and human-readable format.
The full range of medical devices extends from low-risk disposables, such as class I devices (elastic bandages, gloves, etc.) through class II moderate risk devices (surgical sutures, infusion pumps, hearing aids, etc.) to class III high risk devices (pacemakers, artificial joints and other implants).
All of these medical devices require UDI coding. Various technologies are available for applying the UDI on the label, the packaging or the device itself, depending on the material.
Coding and marking solutions for UDI coding on medical devices
- DuPont™ Tyvek®: Videojet Thermal inkjet (TIJ) printers, thermal transfer overprinters (TTO) and UV laser marking machines are ideal solutions to apply UDI codes on medical device packaging made of Tyvek®. The UV laser marking system delivers high-contrast, permanent codes that are resistant to abrasives, chemicals and sterilization processes allowing for lifetime device traceability.
- Pouches: Pouch packaging can be made of various materials, such as Tyvek®, medical paper, metal foil or film. Videojet TTO, TIJ and Continuous Inkjet (CIJ) printers are best suited for UDI coding on various pouch materials.
- Stainless steel: Many medical devices contain stainless steel components. To directly mark medical devices containing high-density materials such as metal, aluminum, stainless steel and plastics, fiber laser marking systems are commonly used due to their ability to produce permanent, crisp codes that withstand intensive wear and repeated sterilization.
- Application Note
- Infographics